Now that we have seen the basic principles in part 1, it is time to discuss the design concerns for a practical system. The first thing that you need to know is what you are designing for, what influences there will be on the system and how these will change over time. After gathering all the necessary information, the ventilation system can be designed and built along two separate lines: horizontal and vertical ventilation.
Horizontal ventilation refers to the movement of air within a defined area. This is the movement that breaks up thermal layering, quickly redistributing the air and evening out humidity levels. In this situation, since the plants are being grown in an environment that is protected from all aspects of nature, the air will become warmer in the vicinity of heat sources such as lights, fan motors and outside walls, and lose heat next to areas or objects that are cooler, known as sinks. If the air is allowed to sit, without moving, the air that has acquired energy will rise, and as it loses energy, it will slowly sink. In the process it will form layers of air molecules that are at a similar temperature. This is termed heat stratification, and horizontal movement is required to mix these layers and allow an even temperature in the growing area, that can be adjusted evenly to cool or heat as the need arises.
Removing micro climates
The leaves of the plant have micro pores located on their surface, through which the water transpires. This is what drives the movement of water from the roots to the top of the plant and moves nutrients internally within the plant. Plants use both oxygen and carbon dioxide, which move in and out through these pores. It is possible, when there is very little air movement, for a build-up of these gases trying to move in and out at the same time. These microclimates (also known as barriers) have to be eliminated to allow the plant to develop at the optimum rate. Horizontal mixing of the air in the grow room eliminates these microclimates, increasing the efficiency of the movement of these gases in and out of the leaves.
Requirements
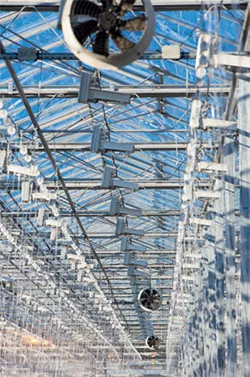
The requirements for horizontal air flow are simple to define but less simple to achieve. The air in the growing area, the area occupied by the plant(s), is the target that needs to be moved. Moving the air in the rest of the room is a good idea but air circulation near the ceiling will add to the heat load since most of that air is warmer than in the growing area, and the floor is liable to harbour more fungal spores or insects. How the air is moved will determine the stress on the plants. In the end, there are really two ways to induce this air flow, the first being the use of air currents produced when removing and replacing the air in the room and the other through a separate, dedicated device such as a smaller fan or the newer high-efficiency horizontal fans (HFs) that are designed to create a small vortex effect in the target zone. The fact that the air exchange air flow is not constant if it is also used to regulate temperature, and the need for horizontal air flow 24 hours a day throughout the crop cycle, means that a separate device is required.
Speed of air movement and distribution
The amount of power needed to change the air in a room several times a minute for cooling purposes will cause air currents that are too strong and can easily cause excessive stress and possibly damage to the plants. When using both a horizontal system and a vertical or exhaust system, there can be a cumulative air pressure/ speed effect that must also be monitored. The ideal speed of circulation should produce a gentle movement of all leaves in the grow zone. This will ensure proper mixing of the air without stressing the plants too much. Where possible, use two wall-mounted fans in smaller areas that are placed at the level of the plants and face in different directions. This will create a rotation in the air mass which allows for the best distribution in the grow zone. In bigger areas, HF fans create a strong force but smaller volume so that, while being very effective at creating localised circulation, this will not be strong enough to impact the plants directly. These are usually placed so that the air flow from the fan is directly above the top of the plants. Creating a stronger vortex just above the plant tops creates the gentle movement in the leaf zone that is desired. This type of action is really impossible with the vertical systems which must also be designed to move all the air in the room or area not just that located in the growth zone.
Vertical Ventilation
Vertical ventilation is a term used to mean that air that is moved out of the grow area and treated, before being returned or replaced by air from another location. Unless the system is designed to supply and extract the air to and from the floor and ceiling, all air flow is horizontal, so the implication in this system is that air is moved across several levels and not across the same level. The air in an area used for plant production must be changed on a regular basis in order to avoid a whole range of issues. Changing the air alters the temperature and humidity, and replaces the gases that are being depleted in an airtight space, such as carbon dioxide. Although horizontal ventilation will mix the air and therefore moderate temperature, humidity and gas ratios by mixing the air across the entire room, it will not remove or add heat, humidity or replace the gases that have been used up. Air exchange is the only real answer.
Open and closed systems
There are two ways to implement a vertical system: either open, meaning that either the system draws in air from a different area which replaces the air in the target area; or closed, meaning the air never actually leaves the growing area and is treated in situ. Treating the air - cooling or heating it, humidifying or dehumidifying it, and replacing depleted gases - is important in both systems, but is absolutely essential in a closed system. Depending on the need to regulate the environment in the growing facility and the needs of the crops produced, the air movement through exchange, in either an open or closed system would determine the exact design of the system.
Closed systems
A closed system will be used in situations where contamination, either biological or environmental through ozone or other industrial pollutants, must be avoided; contact between the air in the interior and the exterior is carried out separately. The area air is removed, treated and returned to the area.
Open systems
An open system draws its fresh air supply from an exterior source such as a controlled room or the exterior. It can be used directly to cause a change in temperature, humidity, and gas content, or it can be treated to cool, heat, humidify, or dehumidify the air before it is supplied to the growing area. This air is then drawn through the area to remove the old air, at a rate that can make a difference. While it is drawing the stale air out of the room, the factors that have brought about the undesired change in temperature or humidity continue to occur. The rate at which this new air can rectify these continuing undesirable effects and remove those that have already built up will determine the rate of air exchange required. This must also occur fast enough to make a difference. There are formulas for calculating humidity and heat loads and the flow rates that are needed to cause a change.
Designing the system
The designer needs to understand what the heat gain or loss for the area is, usually calculated in BTUs or British Thermal Units. Once the required number of BTUs is known, the designer can build a system that will be able to maintain a steady set of values in temperature and/or humidity based on the difference between the worst case scenario and the parameters that conditions must remain within.
Temperature
If the indoor temperature under lights in the summer will reach a maximum of 49°C and the maximum temperature at which the plant should be kept is 32°C then the system must be able to alter the temperature by a differential of 17°C. Heating can be measured in a similar way, and humidity too, although it is calculated differently.
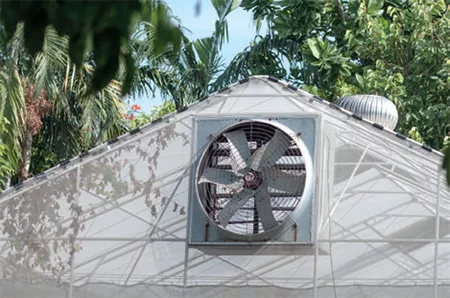
Gas ratios
Gas ratios in an open system are not really an issue as the ratios should always match what is available outdoors, which is always sufficient. In a closed system, it will be necessary to add carbon dioxide during the periods when photosynthesis occurs, since the existing CO2 will be used up in a very short space of time, so fast as to begin to slow down the plant’s metabolic processes within a couple hours. Oxygen, on the other hand, while also needed by the plant at normal life levels, is released in heavy enough concentrations during the fixing of the carbon in the CO2 to supply what is needed.
Which components?
The exact requirements of the system will determine which components will be used. In a closed system, the ability of the environment will determine whether an evaporative cooling system would work well enough or an HVAC unit will be required. The need to move a certain volume of air will determine the size of the ducting and the fans. Open systems work either by drawing in air from the outside into the target area. If the air needs to be cooled and humidified, an evaporative cooling system might be an answer (known as swamp chillers, in some locations, and which can also be used in a closed system). The calculations for these types of systems should be carried out accurately to ensure that a system is both functional and cost-effective. All the factors that would affect a system must be known, and that includes restrictions such as bends in the ducts and any filters used. It is also usually critical to use fans on both the exhaust and input sides to ensure good air movement and balance the pressure in the room.
Controls
Controls for the automation of these systems are also a big concern and cannot be forgotten in the rush to finalise a system. Unless the grower or a grower’s representative can afford to watch a thermometer, a hygrometer, and a CO2 monitor 24 hours a day for months on end, a device to control the operation of the vertical ventilation based system will be needed for either an open or closed system. The horizontal system tends to remain active all the time so a controller is not necessary other than an on/off switch. The minimum that any system will need is a thermostat to regulate the cooling system. A separate thermostat will be needed to regulate a heating system that may be linked to the vent system. In tight rooms used for growing, a humidistat is also a great idea, one that operates the vent system when humidity rises above a certain specified level. It might also be desirable to be able to set different values for a night cycle, especially for temperature. Some systems, especially at certain times of the year, may require cooling during the day and heating during the night, especially in greenhouse environments.
In closed systems, where certain gases like CO2 are released to supplement or raise ambient levels, a gas monitor is also a good idea, especially one that triggers an alarm if the regulation of the gas fails. Adding CO2, while positive for the crop, can be costly and will be less effective if too much is used. It also becomes dangerous to employees and growers if levels rise too high when people are present. A CO2 controller adds value by ensuring that the ventilation pattern never exhausts the gas or that it is added at a certain time in a system that regulates temperature or humidity.
Keep it simple
Everything needs to work together in order to be effective. It is always best when controls can be integrated into a single or dual set of controls. It must also be understood that the KISS principle applies here as well, and the smaller the growing room, the less complicated the system should be. The simpler the controls, the less chance of error or failure. Temperature, humidity and gas injection are controlled by the use of set points so that, when a grower requests, say, a 22°C temperature for cooling, the system will switch itself on when the temperature rises a few degrees above this and run till it gets a few degrees cooler. This allows the system to work more efficiently; very precise control is not needed and will cause the system to constantly click on and off within a single degree or less of temperature change.
Ventilation is certainly not the easiest aspect of growing, but it is an essential aspect of controlling the growing environment for the benefit of the plants. It cannot be neglected in the rush to produce and is fundamental within the overall design of the grow space. Proper care must be taken when designing the installation to ensure functionality… and functionality means success!